On the afternoon of October 19th, Professor Yang Haicheng, chief engineer of the China Aerospace Science and Technology Group and a doctoral tutor, pointed out in the academic report of Liaoning Transportation College: "With the continuous deepening of the 'Internet' thinking, the enterprise is developing into a new platform. The company is moving forward. Personalization is the latest trend in industrial development in the future. Like in the Tiangong 2, there will also be 3D printers for the replacement and repair of the components of the Tiangong itself!"
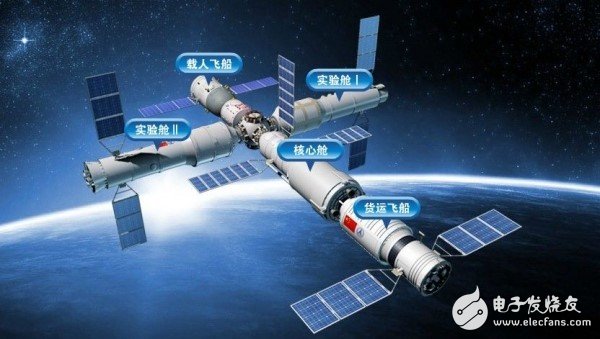
Tiangong 2
As we all know, China Aerospace 60 years, October 19, 3:31, Shenzhou 11 spacecraft and Tiangong 2 automatic rendezvous and docking success. The Tiangong 2 Space Laboratory has been successfully launched at the Jiuquan Satellite Launch Center on September 15, 2016 at 22:04:09. The big improvement is that the equipment is more luxurious, the load is increased, the internal environment is better, and its system design is modular, which means that it can be quickly replaced and in-orbit repair when there is a problem, which belongs to the domestic space field. The first. Tiangong 2 uses a 3D printer to achieve quick replacement and repair of its own components.
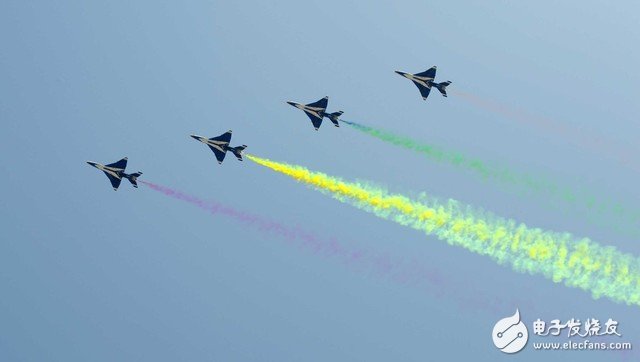
Air echelon
In fact, 3D printing is not the first time in China's aerospace industry. In the aircraft used in the air squad that commemorated the victory of the Chinese People's War of Resistance Against Japanese Aggression and the 70th anniversary of the victory of the World Anti-Fascist in 2015, there is no shortage of 3D printing technology. Out of the parts and components.
As Zhang Feng, chief engineer of the Ministry of Industry and Information Technology, said at the inaugural meeting of the China Additives Manufacturing Industry Alliance, "China's additive manufacturing technology research is not too late, and some aspects are still in the world's leading position." China's aviation industry is applied to 3D printing technology. Not only do several types of aircraft use 3D printing components, but some technologies have reached the world's leading level.
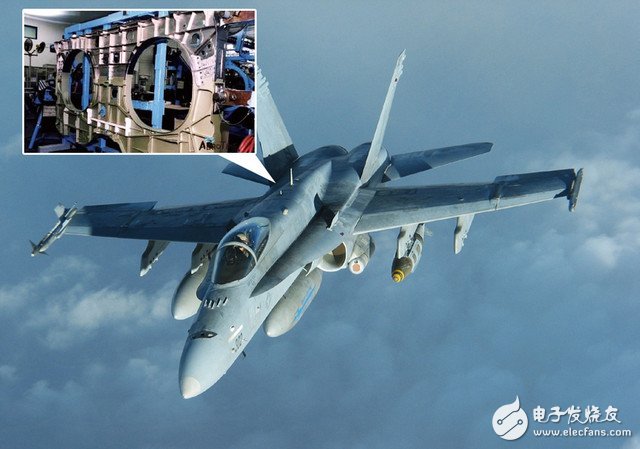
F/A-18E fighter aircraft produced by American Aeromet Company
For example, in the research of laser rapid prototyping technology for metal parts, China began in 1999, ten years later than the United States. However, in the application of research results, the United States has been unable to achieve breakthroughs. In 2005, the F/A-18E fighter aircraft produced by American Aeromet Company failed due to the strength problem test. Subsequently, the company failed to produce a large-scale complex titanium alloy component with performance to meet the main bearing requirements, and failed to achieve a valuable application market and closed down. China has already possessed the technology and capability of using laser to form complex titanium alloy components of more than 12 square meters, and has become the only country in the world to master the manufacture and application of large-scale main bearing components for laser-formed titanium alloys.
In the traditional fighter manufacturing process, after the 3D model of the aircraft is designed, long-term investment is required to manufacture the hydroforming equipment. After the additive manufacturing technology of 3D printing, the forming speed and application speed of the parts can be greatly improved. improve. According to the data, it takes 10-20 years to manufacture an aircraft model, and it takes at least 3 years to apply 3D printing technology. It is enough to prove that 3D printing technology has an irreplaceable advantage in the complex industry.
In fact, 3D printing technology has not been able to be manufactured on a large scale due to cost and technical problems, and the global 3D printing industrialization is still in its infancy. If 3D printing technology is still unrealistic in order to completely replace the traditional processing industry, at least it needs to overcome the following problems:
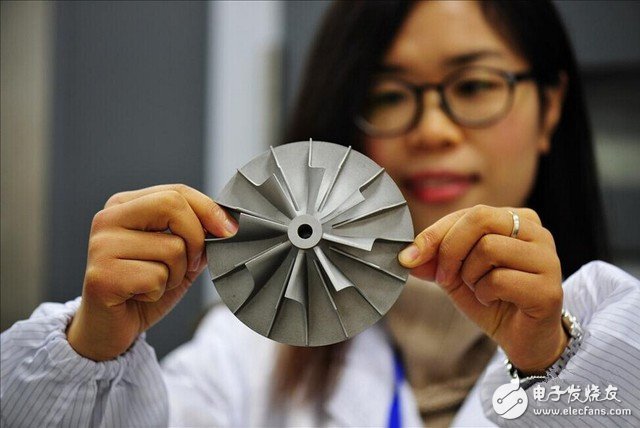
Researchers show aircraft 3D printed parts
In terms of materials, 3D printing is also called “additive manufacturingâ€. It is easy to see that materials are the core of this technology, and materials can be used to make suitable products. The current application of 3D printing products mainly focuses on jewelry, mold models, personalized household products and small-sized parts of automobile airplanes. The materials used are nothing more than resin, plastic, ordinary metal powder. If the industry develops in the high-end, it is necessary to break through the high-performance alloy materials and polymer composite materials, which involve hundreds of materials or even more. Therefore, 3D printing technology can enter the fields of aerospace, artificial intelligence, large complex machinery and biomedical.
On the software side, from the current technical level, consumer-grade 3D printers can only produce simple products like egg racks and combs. And to create a complex industrial product, the technology of three-dimensional design is not something everyone can master. Moreover, in China, there is no 3D design software of its own, and it still needs to pay a large amount of patent fees.
Energy issues, the current energy source for 3D printing is laser, but its production efficiency needs to be improved, especially when processing large-size, high-melting metal products. If you can break through in terms of energy, then printing efficiency can be doubled.
In terms of equipment, the current 3D printer accuracy is about 0.1 mm. If it can break through the nanometer level, it will greatly expand the application range of the industry and bring many revolutionary results.
In general, there is no residue left unrelated to its function in the production process. Once the technology is mature, the production cost will be greatly reduced. Even a person, a computer or a printer may form a “factoryâ€. It is precisely because 3D printing technology has an irreplaceable advantage in such complex industrial fields as aerospace manufacturing. Therefore, China attaches great importance to the development of additive manufacturing technology and industry, not only has introduced a series of policies, but also industrial planning, and also established its Preliminary support system. Personalization is the latest trend in industrial development in the future. It will be a new opportunity in the field of 3D printing, and industrialization will no longer be a problem.
Doorbell speaker:
Doorbell speaker is a kind of micro speaker unit which uses a diaphragm made of Mylar material. Doorbell speakers are of ultrathin design and lightweight and clear voice. It is widely used in building security industry (e.g. intercom, video door phone, intelligent door control..)
There are two types of Mylar speakers from the shapes:
1) Round shapes, we have products from 10mm to 57mm in diameter.
2) Oblong shape, we have products in sizes of 1510/1712/1813-..
FAQ
Q1. What is the MOQ?
XDEC: 2000pcs for one model.
Q2. What is the delivery lead time?
XDEC: 15 days for normal orders, 10 days for urgent orders.
Q3. What are the payment methods?
XDEC: T/T, PayPal, Western Union, Money Gram.
Q4. Can you offer samples for testing?
XDEC: Yes, we offer free samples.
Q5. How soon can you send samples?
XDEC: We can send samples in 3-5 days.
Doorbell Speaker,Doorphone Speaker,Video Doorphone Speaker,Doorbell Wireless Speakers
Shenzhen Xuanda Electronics Co., Ltd. , https://www.xdecspeaker.com