Reverse engineering, also known as reverse technology, is primarily for forward engineering. Forward engineering is a design process from product design to product production, and reverse engineering is a process of recreating a product design technology, which reverses the product through certain techniques and means. Analysis and exploration, through the digital equipment and technology and CAD and other graphics software to construct the surface or entity, form a three-dimensional model, and then deduct and derive the design process of the product's production process, functional characteristics, structural features and technical specifications, and finally produce A design process that is similar in function but different from the original product, from “new to newâ€.
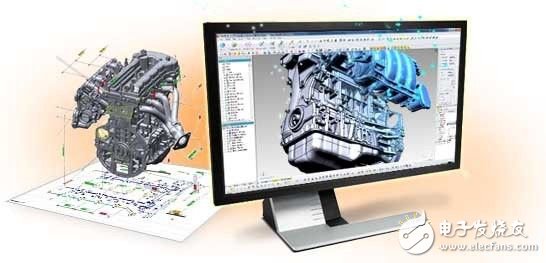
Reverse engineering production process:
For sample 3D mapping → 3D scanning data acquisition → reconstruction model surface → complete 3D model → rapid prototyping → product mold development and production.
Scanning acquisition of existing samples is the most important part of reverse engineering, which determines whether the reconstruction of subsequent model surfaces or entities can be easily and accurately performed. The processing of noise points and outliers will determine the degree of sophistication of the product's later modeling. In this step, the scanner is used to scan the points attached to the upper surface of the sample, and then the image collection is formed by software, and the scanned data is analyzed and integrated by software to complete the data collection. However, professional technicians are required to operate in this process, and existing scanners perform data scanning on large-sized samples such as automobile, motorcycle, etc., because of the limited recognition of product features and constraints. This affects the reconstruction of the product surface. And for large products, from design sketches to sludge models to reverse engineering, longer design cycles can affect product productivity, and a large number of professionals are involved in the process to extend the design cycle, while 3D printing The emergence of technology will shorten the cycle of reverse engineering, reduce the process links, and promote the combination of design and production.
The application of 3D printing technology and product reverse engineering refers to the integration process of product rapid prototyping, product analysis and testing, product reconstruction and manufacturing in the process of reverse deduction and manufacturing of products. The application of 3D printing technology will not only shorten the product development cycle, but also facilitate product analysis and production. 3D printing technology and reverse engineering integration process: sample → scan data → reconstruct mesh surface → model detection, data analysis → model 3D printing → print product analysis → product mold opening and production, product problems and then return to data scanning, so a cyclic process. In this process, the designer also needs to integrate the data of the preliminary printed products into the analysis, and combine the engineers' suggestions on the product structure to continuously improve the appearance of the product, and finally print the products with high precision and good quality.
The extensive application of 3D printing technology to product reverse engineering is not only reflected in the integration process of the two, but more importantly, based on the mastery of the two technologies, new research methods are developed according to the characteristics of the two, shortening the product development cycle and improving Product development quality, reduce research and development costs.
For the materials used, the details that can be displayed vary depending on the precision of the products printed by the different materials. The low-accuracy to high-precision printing method can make up for the shortcomings of the current product details, which requires the digital model to have a deep understanding of the product designer's sketches. The digital modeler can create a simple three-dimensional model through software, and print the low-precision grass model by the 3D printer. After the product designer has refined the sketches of the product lines and details, they will be handed over to the digital model engineers and engineers for processing and efficiency enhancement. After such a cycle, the product development cycle will be greatly shortened, product development costs will be reduced, and efficiency will be improved.
For product development, many design teams use a combination of forward and reverse engineering, and in such a design environment, 3D printing technology can give it a huge advantage. The combination of forward and reverse engineering can make up for the deficiencies in the design process of both parties to a certain extent. As a kind of rapid prototyping technology, 3D printing technology needs to be the link connecting positive and negative engineering. In this process, you can first select the low-precision material to print out the designed model according to the forward engineering process. For some details, the product designer will refine it, and the oil molder will improve the printed model to the overall appearance. After the determination, the surface information that needs to be optimized is scanned through three-dimensional scanning, and processed by the digital modeler and the engineer to print a high-precision model and handed over to Party A. This workflow balances the role of the designers, weakens the process of scraping the mud model, shortens the cycle of the entire process, and takes advantage of 3D printing technology, which is conducive to product development and production.
Harvester Drive Wheel,Belt Drive Pulley,Power Take-Off Shaft,Agricultural Gearbox
Changzhou Youeryou Trading Co., Ltd. , https://www.farmpartssupplier.com