The Internet of Things (IoT) is a term used to describe everyday object collection and data analysis on the network to simplify and automate processes. But once you start designing a specific IoT project, you realize that the benefits and challenges of the IoT vary from project to target. If you are designing an IoT project in an industrial environment, you will face many very different challenges.
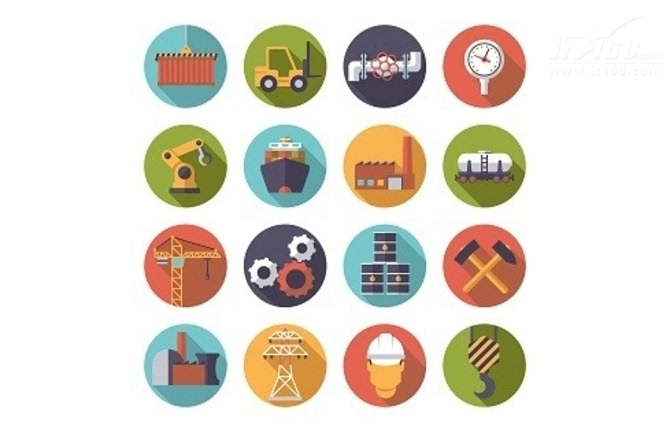
The Industrial IoT uses sensors to collect data to speed processes, increase efficiency, and ultimately reduce the overall cost of a product or service. Compared to Other types of Internet of Things, there are several ways in which industrial IoT deployments are significantly different.
First, the physical environment of industrial connected equipment can vary greatly. Plants, mines and substations that have been in operation for many years are not designed to accommodate the sensitive sensor equipment required for the Internet of Things, which means that sensors installed under harsh conditions such as HVAC, ventilation and power supplies are not ideal.
Second, while technical operations are indeed part of most industries today, the hardware, software, and protocols used are quite different from those we use at the enterprise or consumer level. On the enterprise side, we usually use IEEE and ITU-sponsored agreements. However, manufacturing protocols and platforms are promoted by standards organizations such as the Manufacturing Enterprise Solutions Association MESA and the International Electrotechnical Commission (IEC). Therefore, one of the main challenges facing industrial IoT is to transfer its own unique application platform and data extracted from industrial systems of standard protocols to enterprise systems.
Therefore, before starting the Industrial IoT project, please understand the following eight key issues.
1. Data collection and analysis
Although almost all IoT projects involve the collection and analysis of big data, industrial IoT deployments have their own unique characteristics. Data types, collection methods, and data analysis can come from sensors and software deployed in highly complex and customized machines that can be deployed locally, regionally, or globally. Regardless of the size of these sensors, each industrial IoT deployment will vary in the content, manner and cause of data collection.
2. A challenging environment
Some industrial IoT deployment environments may be simpler, and you should be thankful because you can deploy sensor facilities in a fully controlled climate. But in most cases, sensors and other sensitive network equipment are deployed in harsh environments, including high temperatures, extreme cold, high humidity, and poor ventilation. Clean energy is also a big problem. In many cases, the Industrial IoT needs to reinforce IoT sensors and network hardware to withstand the challenges of these physical environments.
3, quality control
One of the key differences between the Industrial Internet of Things and other types of Internet of Things is that the vast amount of data collected for the Internet of Things involves automated quality control processes. Quality control is an important aspect of the production of most industrial products, but the type and method of collection of quality control data is highly specific to the industry.
4. Energy efficiency
Another driving force behind the Industrial Internet of Things is the discovery and automation of energy efficiency in a variety of ways. This involves the implementation and collection of smart sensor data in HVAC and lighting systems, the implementation of artificial intelligence into plant equipment to keep them at an optimal level, and higher energy efficiency by upgrading specific components.
5. Improve supply chain visibility
Before becoming Apple's CEO, Tim Cook was known as the manufacturing supply chain guru. Regardless of the industry in which you work, improving supply chain processes is critical. However, identifying areas that can be improved in the supply chain is easier said than done. Many supply chain processes are computerized with built-in digital silos, which leads to blind spots in the supply chain and will cost more. Many industrial IoT projects are designed to provide end-to-end supply chain visibility.
6, modified equipment
In many cases, industrial IoT projects will involve the use of IoT sensors to retrofit industrial equipment, including manufacturing equipment, forklifts and storage containers. While some IoT projects may be using new devices, most projects will need to update traditional processes and tools to enter the IoT space.
7. Industry specific applications and protocols
If you have never been involved in industrial IT, you may have never heard of protocols such as OPC, MQTT DDS or AMQP, and you will not process applications based on SCADA and MES platforms. All of these are common applications and protocols used in the industrial IT world. So the challenge will be to connect these industrial devices and platforms to enterprise applications and data storage mechanisms.
8. Consolidation of industrial IT and enterprise IT
Although industrial IT has been around for quite some time, in many cases, enterprise IT and industrial IT work independently. For example, if the manufacturing device is network connected, the network is initially built into a closed system that never touches the corporate network. However, for the Industrial Internet of Things, the two must work together as a unit. But this is to be difficult because the technology and security mechanisms between the two IT networks are different. Fortunately, organizations such as the Industrial Internet Alliance (IIC) are developing a framework to help fill this gap.
Other
Wenzhou Hesheng Electronic Co., Ltd. , https://www.heshengelec.com