With the segmentation of the drone market, the industry's application of the drone market has been growing rapidly in the past two or three years. Many companies want to grab this big cake. However, some manufacturers in the market have entered the industrial drone market without investing in research and development. The market is equipped with industry and drones. Many of the fish are mixed. The quality is also uneven. It only pays attention to the price to buy carbon fiber racks. It takes time and energy to lose money.
The manufacturing process of industrial-grade UAV racks is not as simple as ordinary people think. It is not the idea of ​​a model airplane to do industrial-grade drone racks, and it is not done in a short time.
Must be realistically overcome various technical difficulties, repeated trials of sleepless nights to make products that satisfy customers.
Ok, I won’t say more, I’ll order some dry goods.

This is the part of the fuselage display picture, our fuselage is a whole, rather than some manufacturers do the upper and lower fuselage and then glue together, in the case of cold and heat, it is prone to cracking
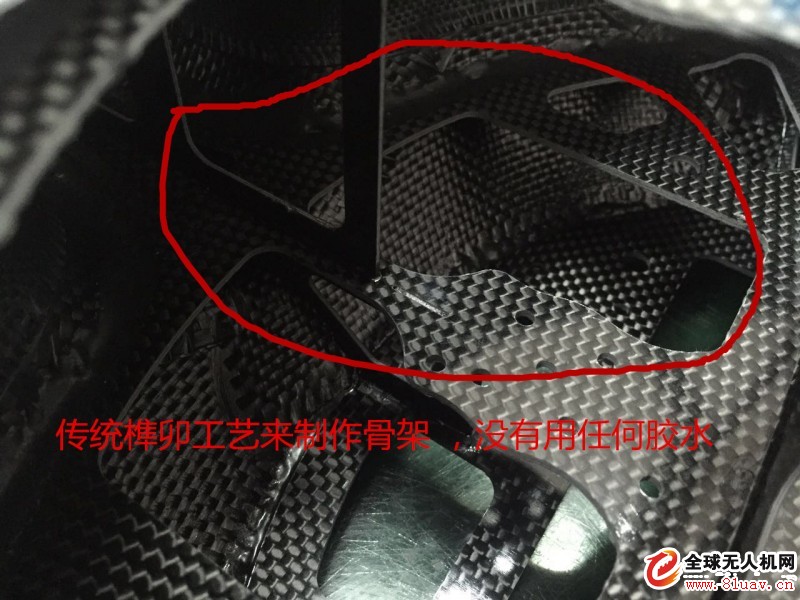
The skeleton inside shows the pictures. Our skeletons are all made by the traditional craftsmanship. All of them are snap-fitted together. The body is put in advance, so that it is a whole, not a second paste. .
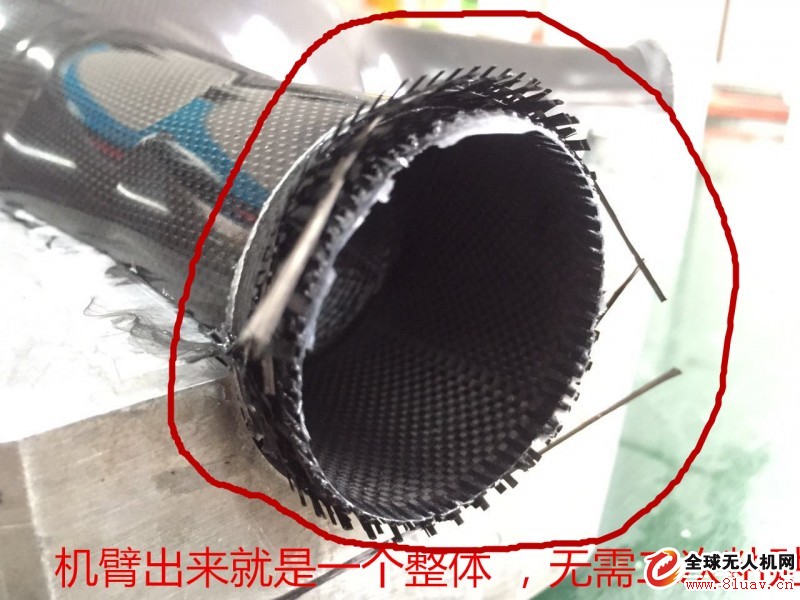
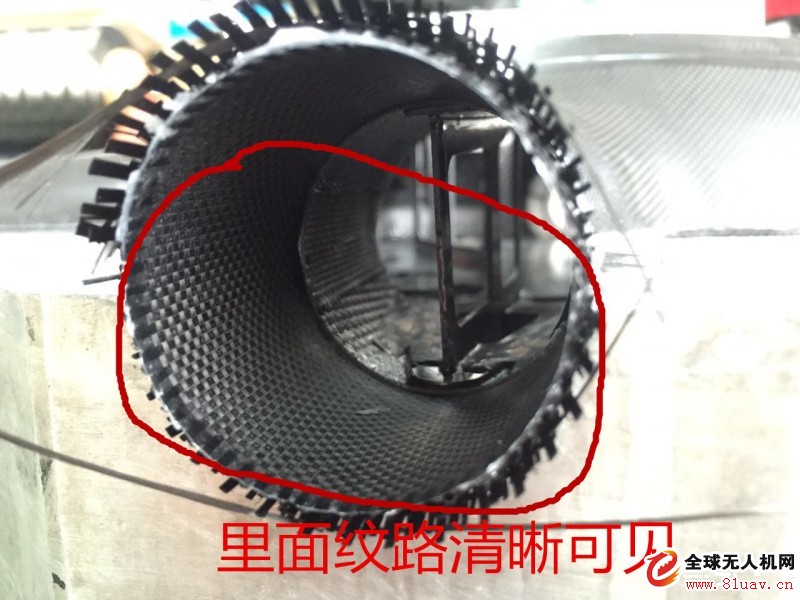
The lines inside are clearly visible, traditional craftsmanship is made, and the hot pressing process does not see the so-called lines. The hot pressing process is made up of two semi-finished machine arms and then glued together again, if there is a crash
The glue paste will be completely cracked.
The picture is made by the arm. The arm is placed in the mold with a piece of carbon cloth. It is a complete arm in the oven. The rough edge part needs cutting machine for cutting.
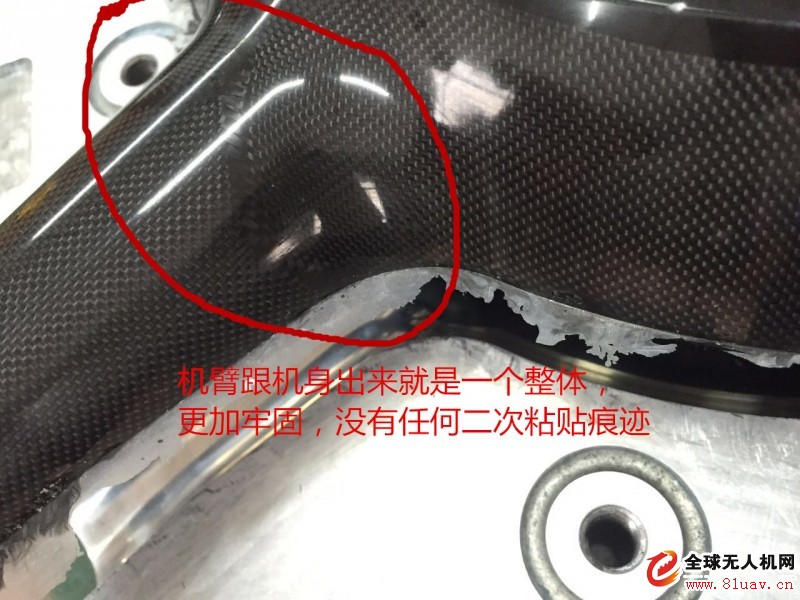
The lines of the arm and the body are clearly visible. They are all lapped together with a piece of carbon fiber cloth. The surface looks shiny and the lines are clear. Pressing with your fingers is flexible and flexible.
The layout of the battery compartment inside is very simple and neat. There are integrated circuit boards inside, and various signal line power lines are carefully arranged. In addition, we also do shield electromagnetic interference to avoid electromagnetic interference to the interference of the flight control remote control signal.
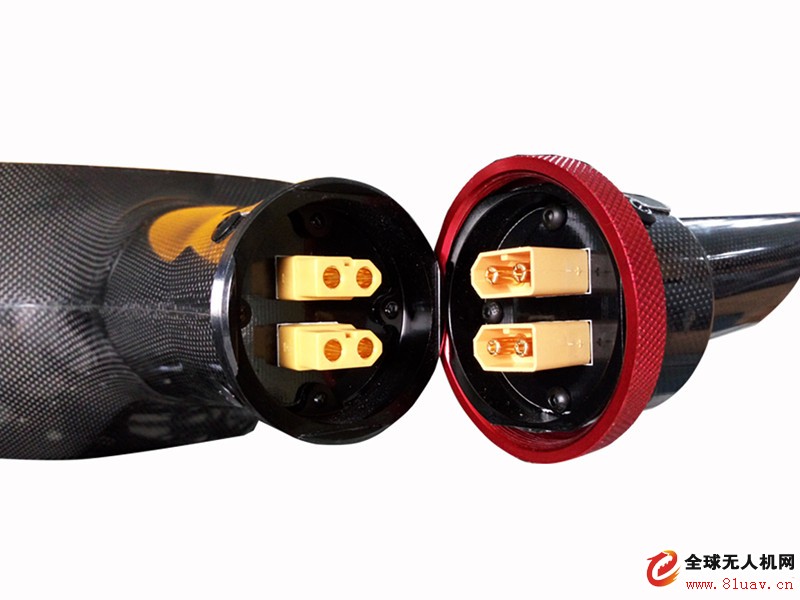
The display of the arm and the fuselage connection, we use a small circuit board and XT60 connector to connect, with flange screw for quick removal and installation.
The manufacturing process of industrial-grade UAV racks is not as simple as ordinary people think. It is not the idea of ​​a model airplane to do industrial-grade drone racks, and it is not done in a short time.
Must be realistically overcome various technical difficulties, repeated trials of sleepless nights to make products that satisfy customers.
Ok, I won’t say more, I’ll order some dry goods.

This is the part of the fuselage display picture, our fuselage is a whole, rather than some manufacturers do the upper and lower fuselage and then glue together, in the case of cold and heat, it is prone to cracking
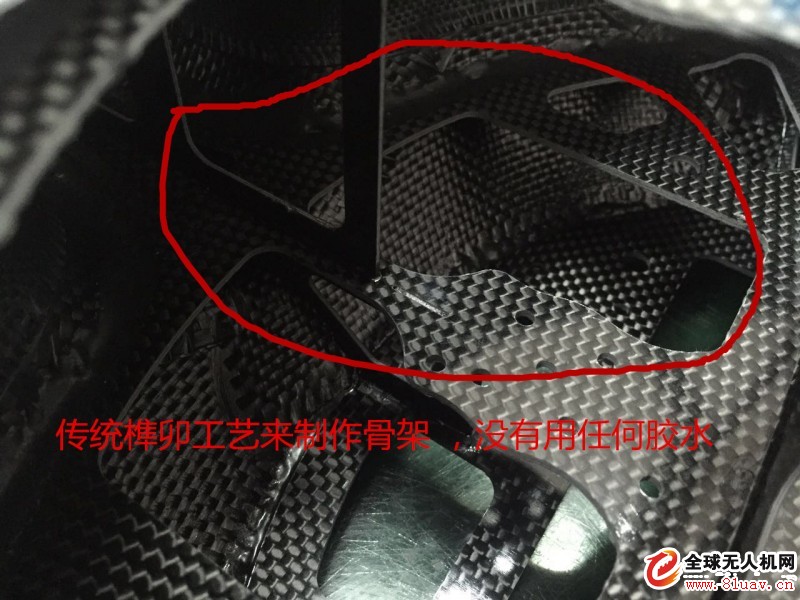
The skeleton inside shows the pictures. Our skeletons are all made by the traditional craftsmanship. All of them are snap-fitted together. The body is put in advance, so that it is a whole, not a second paste. .
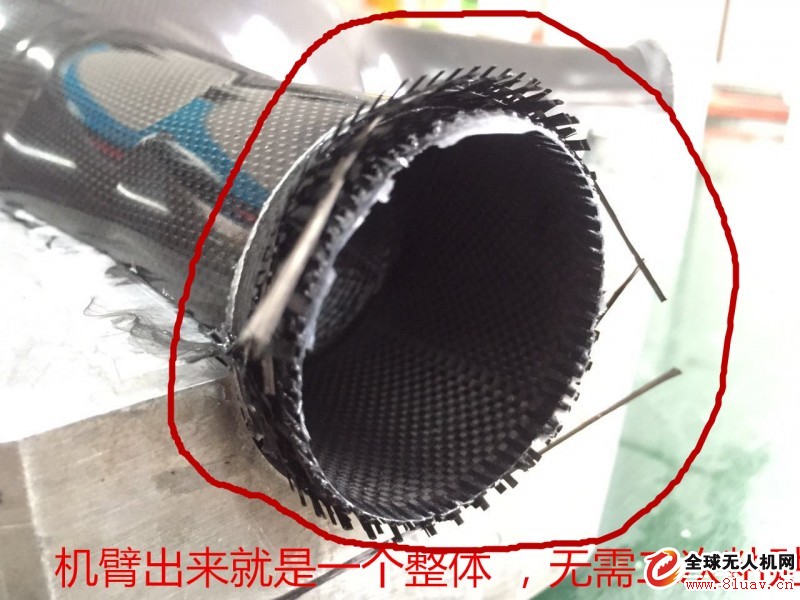
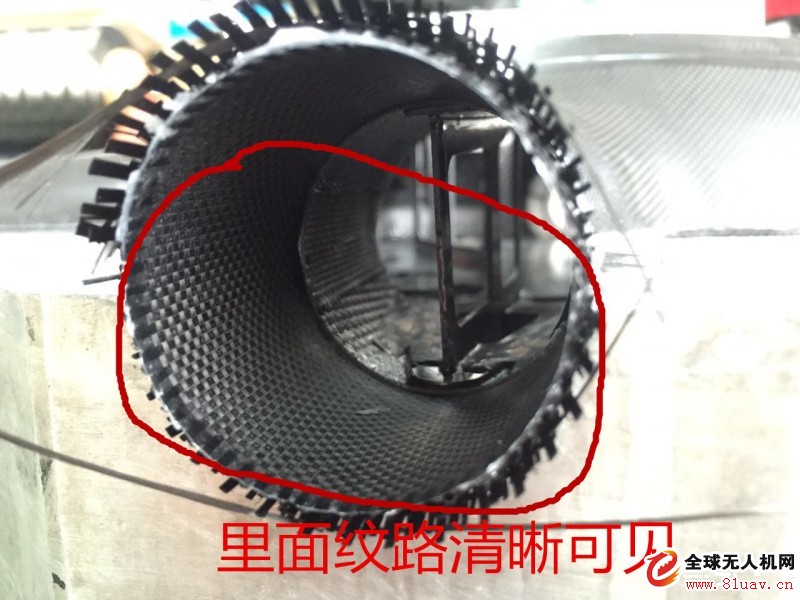
The lines inside are clearly visible, traditional craftsmanship is made, and the hot pressing process does not see the so-called lines. The hot pressing process is made up of two semi-finished machine arms and then glued together again, if there is a crash
The glue paste will be completely cracked.
The picture is made by the arm. The arm is placed in the mold with a piece of carbon cloth. It is a complete arm in the oven. The rough edge part needs cutting machine for cutting.
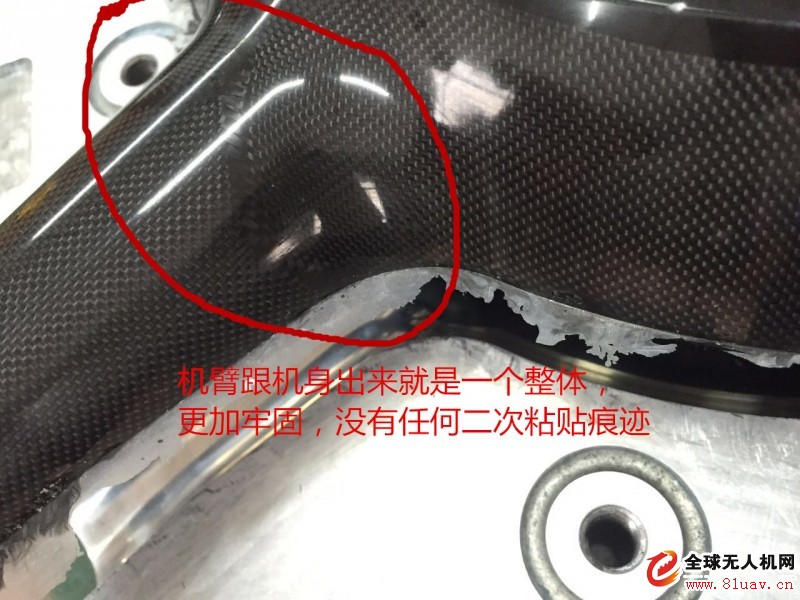
The lines of the arm and the body are clearly visible. They are all lapped together with a piece of carbon fiber cloth. The surface looks shiny and the lines are clear. Pressing with your fingers is flexible and flexible.
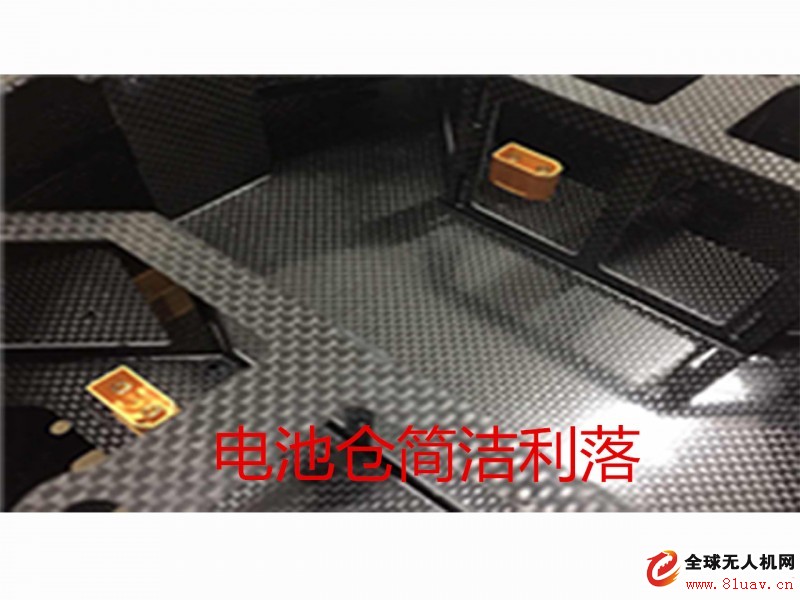
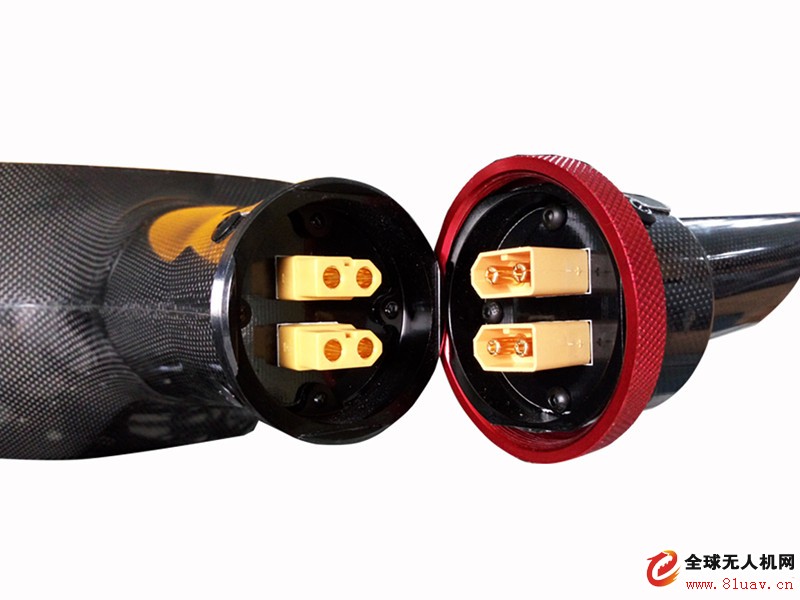
The display of the arm and the fuselage connection, we use a small circuit board and XT60 connector to connect, with flange screw for quick removal and installation.
For Moto Glass,Moto G50 Screen Glass,Motorola Edge Screen Glass,Motorola Front Glass
Dongguan Jili Electronic Technology Co., Ltd. , https://www.jlocaglass.com