Abstract: Many devices require a user interface to adjust the temperature, backlight intensity, and power supply voltage. This user interface needs to be able to avoid misoperations in key adjustments. If a digital potentiometer is used in these devices, the designer can avoid incorrect adjustment operations through a simple hardware interface.
Overview Using a microcontroller, you can write a program to suppress the jitter of the input control signal, and extend the delay before the switch is turned off to prevent misoperation. However, using a microprocessor to implement a good user control interface requires lengthy programming and verification processes. This article uses the digital potentiometer to design a simple hardware solution, which can ensure the adjustment operation of the system when necessary.
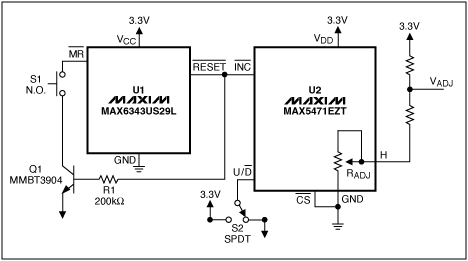
Figure 1. This design uses an extended delay manual reset device and a 32-tap non-volatile digital potentiometer to implement the key-hold switch for system adjustment operations.
Realization of key-hold control. Figure 1 is a schematic diagram designed in this paper. Users can implement increase / decrease control through a friendly interface. In the design, a manual reset device with extended delay (U1, MAX6343) is selected to avoid the influence of key misoperation, and a 32-tap nonvolatile digital potentiometer (U2, MAX5471) is used to increase / decrease VADJ. VADJ can be used for the feedback loop control of the power supply or backlight converter, and the data can be read directly through the A / D converter.
For the user interface, the switch S2 first sets the increase and decrease control commands, and the key hold switch S1 starts the control process.
The / MR input of the MAX6343 requires a settling time of 6.7s to confirm the detection of a valid / MR signal. Therefore, after the user presses the switch S1 and holds it for 6.7s, / RESET goes low.
The change from high to low on the MAX5471 / INC pin causes the output value of the variable resistance of the digital potentiometer to increase or decrease by 1/32 (because the MAX5471 has non-volatile memory, even when there is no power supply. Can keep the setting data in its memory).
In order to prevent the user from touching S1 by mistake, increase the transistor Q1, you can reset the MAX6343 6.7s timer after each reset or increase / decrease control command. The user can control S1 in this way until the required set voltage (VADJ) is reached. This design can increase / decrease control every 6.7s, because the / MR input of MAX6343 has a 50kΩ pull-up resistor, Q1 can choose a general-purpose NPN tube similar to MMBT3904, choose R1 resistor of 200kΩ, to ensure that when / RESET is high The transistor is saturated.
Figure 1 shows a typical feedback network. Resistors R3 and R4 are connected in series with the variable resistor MAX5471 (RADJ). Determine the choice of values ​​according to the actual application; if R3 = R4 = 200kΩ, the VADJ can be calculated using the following formula:
VADJ = ((RADJ + R4) / (R3 + R4 + RADJ)) x 3.3V (Formula 1)
When RADJ = 0Ω (minimum setting): VADJ = 1.65V
When RADJ = 50kΩ (maximum setting): VADJ = 1.83V
Therefore, (1.83-1.65) / 32 (level) = 5.7mV / level
Conclusion Using the circuit provided in this application note, a simple hardware solution can be used to avoid misuse of the system control. The user only needs to select the increase / decrease control, press and hold the switch S1, and can slowly use a good user interface to perform System adjustment.
Overview Using a microcontroller, you can write a program to suppress the jitter of the input control signal, and extend the delay before the switch is turned off to prevent misoperation. However, using a microprocessor to implement a good user control interface requires lengthy programming and verification processes. This article uses the digital potentiometer to design a simple hardware solution, which can ensure the adjustment operation of the system when necessary.
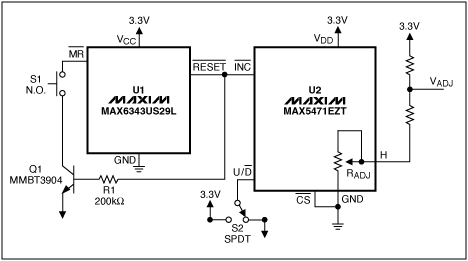
Figure 1. This design uses an extended delay manual reset device and a 32-tap non-volatile digital potentiometer to implement the key-hold switch for system adjustment operations.
Realization of key-hold control. Figure 1 is a schematic diagram designed in this paper. Users can implement increase / decrease control through a friendly interface. In the design, a manual reset device with extended delay (U1, MAX6343) is selected to avoid the influence of key misoperation, and a 32-tap nonvolatile digital potentiometer (U2, MAX5471) is used to increase / decrease VADJ. VADJ can be used for the feedback loop control of the power supply or backlight converter, and the data can be read directly through the A / D converter.
For the user interface, the switch S2 first sets the increase and decrease control commands, and the key hold switch S1 starts the control process.
The / MR input of the MAX6343 requires a settling time of 6.7s to confirm the detection of a valid / MR signal. Therefore, after the user presses the switch S1 and holds it for 6.7s, / RESET goes low.
The change from high to low on the MAX5471 / INC pin causes the output value of the variable resistance of the digital potentiometer to increase or decrease by 1/32 (because the MAX5471 has non-volatile memory, even when there is no power supply. Can keep the setting data in its memory).
In order to prevent the user from touching S1 by mistake, increase the transistor Q1, you can reset the MAX6343 6.7s timer after each reset or increase / decrease control command. The user can control S1 in this way until the required set voltage (VADJ) is reached. This design can increase / decrease control every 6.7s, because the / MR input of MAX6343 has a 50kΩ pull-up resistor, Q1 can choose a general-purpose NPN tube similar to MMBT3904, choose R1 resistor of 200kΩ, to ensure that when / RESET is high The transistor is saturated.
Figure 1 shows a typical feedback network. Resistors R3 and R4 are connected in series with the variable resistor MAX5471 (RADJ). Determine the choice of values ​​according to the actual application; if R3 = R4 = 200kΩ, the VADJ can be calculated using the following formula:
VADJ = ((RADJ + R4) / (R3 + R4 + RADJ)) x 3.3V (Formula 1)
When RADJ = 0Ω (minimum setting): VADJ = 1.65V
When RADJ = 50kΩ (maximum setting): VADJ = 1.83V
Therefore, (1.83-1.65) / 32 (level) = 5.7mV / level
Conclusion Using the circuit provided in this application note, a simple hardware solution can be used to avoid misuse of the system control. The user only needs to select the increase / decrease control, press and hold the switch S1, and can slowly use a good user interface to perform System adjustment.
Optical Prism,Dispersion Prism,Si Right Angle Prism,Chandelier Prisms
Danyang Horse Optical Co., Ltd , https://www.dyhorseoptical.com