1 Introduction Shenzhen Micro Energy Technology Co., Ltd. has always been committed to the technical innovation and development of the inverter as its mission. In the past 5 years, it has made outstanding achievements in the development and application of high-power and high-performance for low-voltage inverters and high-voltage inverters. Contributing, this article describes the principle of large-capacity high-voltage inverters and their applications in the steel industry.
2 Status Quo of China's Iron and Steel Industry Under the strong national economic development, China's steel industry has entered a stage of rapid development, which has also led to the rapid development of the blast furnace ironmaking industry. The current status of China's ironmaking industry is low concentration, with a large number of blast furnaces (about 900 seats), and about 110 blast furnaces with more than 1,000 m3.
High wind temperature is the main technical feature of modern blast furnaces. Increasing the air temperature is the main technical measure to increase the amount of coal injected, reduce the coke ratio, and reduce production costs. In recent years, the hot blast temperature of blast furnaces in domestic iron and steel companies has risen by 25°C year after year, especially in the new batch of large blast furnaces (greater than 2000m3), and the hot blast temperatures exceed 1200°C, reaching international advanced levels, such as after 2002. The hot blast temperature of Shougang's technological transformation or newly-built blast furnace has achieved a goal of higher than 1200°C. In addition, through the adjustment of parameters such as air volume, wind pressure, air humidity, oxygen enrichment rate, fuel injection, tuyere area, and length, the purpose of increasing production and utilization factor of blast furnace can be achieved. This requires the implementation of the air supply system. Better optimization. Therefore, it is apparent that the motor speed required to drive the blast furnace blower must meet the requirements of a wide speed range and a rapid response, which cannot be achieved through conventional damper adjustment. The improvement of the research and design level of China-made high-voltage inverters and the maturity of manufacturing technologies have made it possible to optimize the air supply system for blast furnace blowers.
2.1 Introduction to Modern Blast Furnace Ironmaking Process The ironmaking process is essentially a process in which iron is recovered from iron-containing compounds such as ore in its natural state. Usually divided into sintering and ironmaking two processes. Sintering: It is a method of supplying iron ore fines to a blast furnace to provide fine material. It is a process that uses iron ore fines, fluxes, fuels, and returning minerals to make a block of smelting raw materials in a certain proportion; Ironmaking: Ironmaking The main purpose of the process is to obtain economically and efficiently liquid iron from the iron ore with the desired temperature and composition.
2.2 Technology Introduction of Blast Furnace Blower The blast furnace blower is the most important power equipment in the blast furnace ironmaking process. It not only directly provides the oxygen needed for blast furnace smelting, but also provides the gas power needed to overcome the blast furnace material column resistance. The blowers used in modern large and medium-sized blast furnaces mostly use centrifugal blowers or axial-flow blowers. In recent years, there has been a tendency to gradually use large-capacity synchronous electric driven blowers. Blast furnace smelting requires that the blower can supply a certain amount of stable air to ensure that the blast furnace burns a certain amount of carbon; the amount of air required is not only proportional to the furnace capacity, but also related to the degree of furnace fortification, generally 2.1 to 2.5 m3 per unit of furnace capacity. The air volume of min is equipped. However, in fact, many blast furnaces take into consideration the development of production, and the equipped fan capacity is greater than this ratio. Therefore, inlet dampers and outlet dampers are generally used for air volume and air pressure control to prevent blower surge. The process flow chart shown in Figure 1.
Figure 1 blower process flow chart
Because of the loss of the damper, the blast furnace blower has low efficiency and large power consumption. Therefore, the use of high-voltage inverters has huge room for energy saving. However, as the blast furnace blower is the most critical equipment for blast furnace production, not only the power capacity of the motor is large, but also it needs to ensure continuous operation. If the blower fails in the blast furnace production process, especially when it exits the molten iron, it will cause a slag filling accident, which will lead to furnace blockage, stop of production, increase of coke ratio, and huge economic losses. Therefore, the domestic metallurgical industry manufacturers are currently implementing blast furnace blowers. There are few cases of high-voltage frequency conversion transformation, mainly because users have doubts about the operational reliability of current high-voltage frequency converters.
Shenzhen Weieng Technology Co., Ltd. accumulated more than 20 years of experience in designing and producing frequency converters, based on a thorough understanding of motor control theory, mastery of power electronics and microelectronics technologies, and integration of micro-processing technologies, independently developed and autonomously developed. The large-capacity high-voltage inverter of intellectual property rights took the lead in breaking the design and production records of domestic high-pressure, large-capacity and high-voltage variable-frequency speed control systems. Micron's R&D technical staff worked together with Party A's production process and technical staff. Based on the principle of high responsibility, seeking truth from facts, sincere cooperation, and many in-depth investigations at the scene, the company has obtained detailed data on the production process. Based on the guiding ideology of preserving safe production for users, it has formulated a comprehensive and thorough troubleshooting backup plan approved by both parties; Micro Energy's large-scale production and manufacturing, strict quality control system, and a large number of stable and reliable metallurgical industry operating results. Obtained the recognition and trust of Party A, and further strengthened the determination of the user's transformation. The user decided to conduct a high-voltage variable frequency speed control transformation of No. 2 ironmaking blast furnace blower in the plant so as to reduce the production cost and improve the production process.
3 Micropower WIN-HV Series High Voltage Variable Frequency Speed ​​Control System Technology Introduction
3.1 Principle and structure of WIN-HV series high voltage variable frequency speed control system
3.1.1 System Principle As shown in Figure 2, the WIN-HV series high-voltage variable frequency speed control system uses multiple power units in series. For a 10 kV system, 9 units per phase are connected in series (6 units per phase for a 6 kV system). Each power unit outputs an AC rms value Vo of 640 V, a phase voltage of 5760 V, and a line voltage of 10000 V.
Figure 2 The principle of voltage superposition and high voltage output
3.1.2 Power Unit Structure As shown in Figure 3, the power unit is mainly composed of a three-phase bridge rectifier bridge, filter capacitor, and IGBT inverter bridge, as well as the control of power device drive, protection, signal acquisition, and optical fiber communication. Circuit. By controlling the operating state of the IGBT, the PWM voltage waveform as shown in FIG. 4 is output. Each power unit with the same current size is completely identical in structure and electrical performance and can be interchanged.
Figure 3 Power Unit Circuit Structure Figure 4 Unit Output PWM Waveform
3.1.3 Input-side WIN-HV series high-voltage variable frequency speed control system uses up to 54 pulses of phase-shifting rectification technology on the 10kV power supply side. The harmonic pollution on the grid side is small, power factor is high, and power factor compensation and harmonic suppression devices are not required. Other electrical equipment on the same power grid does not generate harmonic interference.
3.1.4 The output side is connected on the output side by the L1 and L2 output terminals of each unit. The star connection is used to supply power to the motor. Due to the multiplexed sinusoidal pulse width modulation SPWM technology, the output harmonics are very small. Elimination of the vibration of the blades and bearings eliminates the need for harmonic suppression devices to directly adapt to various motors.
3.1.5 Controller The main control part adopts a dedicated DSP (digital signal processor) plus programmable logic device as the control core to achieve SPWM waveform control and detection, analysis, judgment and processing of various signals. The controller is displayed in Chinese, with display of frequency, current, voltage, fault, etc. The control power adopts two-way power automatic switching technology to ensure the reliability of power supply. In addition, when the control power supply is powered off, the UPS equipped with the system can continue to supply power.
The main control section and the unit control section transmit signals through optical fibers, which can effectively avoid electromagnetic interference and enhance the reliability of the system.
3.2 WIN-HV Series High-voltage Variable Frequency Drive System Function
3.2.1 Starting Mode WIN-HV series high voltage variable frequency speed control system has two starting modes: normal starting and soft starting: Normal starting mode: After the speed regulating system is started in the normal mode, the closed loop or open loop runs at the set value.
Soft-start mode: For high-power motors, this speed control system is used to start the motor without impact current. After the startup is completed, the motor is switched to the power-frequency power supply to complete the soft start of the motor.
3.2.2 Operation mode Closed-loop control: The detection loop obtains the actual value of the controlled variable and compares it with the set value to obtain the deviation signal. The deviation signal is controlled by the PID to control the motor speed and adjust the controlled variable to make it consistent with the set value.
Open-loop control: Open-loop control is selected. The frequency control signal is given by the frequency setting method. The output is controlled by several voltage-frequency ratio curves set according to the load characteristics to control the motor operation.
3.2.3 Frequency Setting Function Operation frequency setting modes include: IPC LCD touch screen digital setting, external 4~20mA, 0~20mA or 0~10V, 0~5V analog signal input given, switching frequency rising/falling Given, the host computer given a variety of given ways to meet the connection requirements of all signal types with the on-site DCS system.
3.2.4 Control Mode Local control: Use the buttons on the touch screen of the industrial computer to implement local control.
Remote control: The system provides digital and RS-485 communication interface, which is controlled by DCS or host computer.
3.2.5 Parameter setting function The torque boost and U/f acceleration curve can be set to suit different load conditions. Up to 2 resonance frequency avoidance areas can be set. Motor protection parameters and output can be set according to site conditions. Quantity function definition settings, etc.
3.2.6 Fault alarm and query function With fault alarm and fault query function, it can improve troubleshooting efficiency and provide convenience for user maintenance.
3.2.7 Operation Status Record and Display The WIN-HV series high-voltage variable frequency speed control system has the function of automatically recording the running status and displaying, and classifies the displayed data to facilitate routine maintenance. At the same time, it can be connected with the host computer through serial communication, upload the operating status information to the host computer, analyze the record data, and print the report.
3.2.8 bypass function Bypass: When the frequency conversion speed regulation system is downed or the frequency conversion speed regulation system is inspected, the motor is directly switched to the power grid frequency operation to improve the adaptability of the entire system and ensure the user load. Continuous operation requirements.
Unit bypass: WIN-HV series high voltage variable speed system is also designed with power unit bypass function. When a unit is overheated, the unit is short-circuited, or the unit is charged, the control system automatically removes the power unit from the system and removes the other two-phase units with the same potential to ensure that the system continues to operate with a certain load capacity. .
3.2.9 Other functions Linkage control: WIN-HV series high-voltage variable frequency speed control system can provide linkage control function according to user needs and control other components in the production process.
3.3 Product Features of WIN-HV Series High-voltage Variable-frequency Speed ​​Control System WIN-HV series high-voltage variable-frequency speed control system is applicable to standard high-voltage (3kV, 6kV, 10kV) three-phase AC motors and has the following features:
3.3.1 Application to China Power Grid, Strong Resistance to Voltage Fluctuation The voltage at the side of the network is not shut down within the range of 85% to 115% of the rated value to ensure continuous operation of the motor.
3.3.2 Soft start, no impact current WIN-HV high voltage variable frequency speed control system soft start the motor, with a linear and quadratic curve form to control the voltage - frequency ratio, each curve in the form of multiple curves for the user to choose. The start time is set by the user. The function of accelerating the overcurrent and speed limit is provided internally to ensure that the motor starts the inrush current and ensures the safe operation of the motor. During the start-up process, the motor speed is automatically searched, and it is not necessary to ensure that the motor stops, and quick start can be achieved without overcurrent impact on the power grid and the motor.
3.3.3 Isolating Technology of Control Power Supply When the system is not connected to high-voltage power, debugging of the whole machine can be performed.
4 Blast Furnace Blower Retrofit Program The 2# ironmaking blast furnace (which is an internal-combustion hot-blast stove) blower is started by the stator string water resistance, and the air volume and the air pressure are adjusted by adjusting the fan inlet damper and the outlet discharge damper damper opening.
4.1 2# 450m3 blast furnace blower and supporting motor parameters:
2# 450m3 blast furnace blower and related motor parameters are shown in Table 1.
Table 1 Motor and fan parameters
Motor Parameters (manufacturer: Shenyang Motor Co., Ltd.)
motor model
Y1050-4
Power Factor
0.9
rated power
7100kW
Connection
Y
Rated voltage
10000V
Shell protection
IP44
Rated current
472A
Insulation class
F
Rated frequency
50Hz
Quota type
S1
Rated speed
1494rpm/min
altitude
Less than 1000
Transmission ratio 1:3.563
Fan parameters (manufacturer: Xi'an Shaanxi Drum Power Co., Ltd.)
Imported air volume
1900m3/min
Shaft power
6235kW
Import pressure
0.096MP
Speed ​​of work
5330 rpm/min
Outlet pressure
0.35MP
Inlet temperature
28°C
4.2 Implementation Plan of Frequency Conversion Reform of Blast Furnace Because of the importance of the blower in the ironmaking process, when the high-voltage frequency converter is inspected or faulty, the automatic blow-cut method is used to make the blower run in the power frequency state and start when the frequency converter is running. The current is very small and will not affect the power grid. It is very convenient for equipment overhaul. The system uses a tow and an automatic bypass device. The device is wired once as shown in Figure 5.
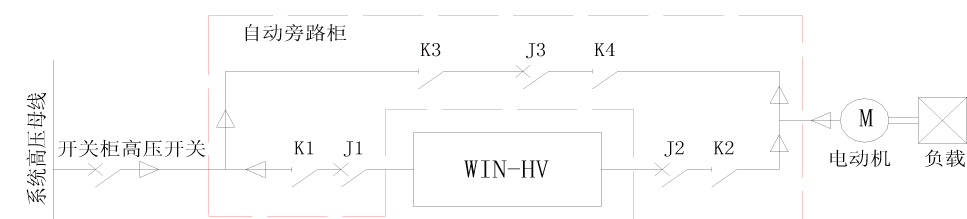
Figure 5 Automatic Switching Mode Wiring Diagram
(1) K1, K2, K3, and K4 have no mechanical locking function, but are manually disconnected during inspection to form an obvious disconnection point to ensure the safety of workers. In the frequency and frequency conversion operating conditions are closed.
(2) The power frequency bypass contactor J3 and the frequency conversion line contactor J1 and the frequency conversion line contactor J2 have an electrical locking function and cannot be closed at the same time.
(3) In the variable frequency operation, J1, J2 are closed and J3 is open. If it is necessary to automatically switch to the power frequency operation, stop the inverter output first, and then trip the user's 10kV switchgear cabinet, then turn off J2 and J1 in sequence by electrical control, and then close J3 to switch the motor to the power frequency side, in the closing switch cabinet. To make the motor run at normal frequency.
(4) J3 is closed and J2 and J1 are open under the power frequency bypass operation. If you need to automatically switch to variable frequency operation, at this time, the electrical line control first trips the 10kV switchgear, then disconnects J3, then closes J2, J1, closes the switchgear, and then starts the inverter, completing the operation from the power frequency bypass. Frequency conversion operation automatic switching.
The operating conditions of the blast furnace blower strictly require its 24h continuous operation, and the trip or shutdown will have a serious impact on the entire production and even the blast furnace itself. Shenzhen Weineng Technology Co., Ltd. has a self-developed speed tracking technology, which provides a reliable guarantee for the free switching of the rotating motor in work/frequency conversion and improves the reliability of the entire system. It has been proved that the automatic bypass program and fault backup solution adopted in the transformation are scientific, safe, and feasible.
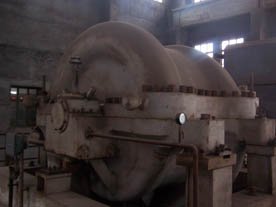
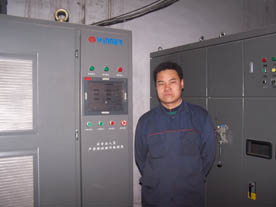
5.1 Economic data of blast furnace technology has been improved after blower energy-saving
During the operation of the 2# blast furnace in a few years after its completion, the blast furnace utilization factor has been hovering around 2.6, and the production between the blast furnaces is not balanced, the furnace condition is difficult to be stable for a long time, and the economic and technical indicators are not going: the pig iron contains [Si] at 0.4 %~0.6%, coke ratio at 450kg/t, pulverized coal injection at 130kg/t, blast furnace gas CO2 content at 11%~14%, and air temperature at 900~1150°C. Compared with the data in Table 2 “Blast Furnace Technical Economic Indicators for National Key Iron and Steel Enterprises,†the gap is very large. Industry experience experimental data shows that: When the pig iron containing [Si] is reduced by 0.1%, the coke ratio can be reduced by 4 to 5 kg/t; the CO2 content is increased by 0.5%, and the iron-smelting fuel consumption can be reduced by 10 kg/t. In particular, when the furnace condition is not smooth and the balance is destroyed, it is difficult to restore to the original level of production technology, and it is impossible to establish and form a set of sound and reasonable air supply operation system.
Data time
2008
2008
2006
2005
2004
Yield: ten thousand tons
39095.27
4699.63
41364.09
34473.20
25185.05
Focal ratio: kg/t
398
392
397
412
427
Coal ratio: kg/t
135
137
134
120
116
Coefficient: t/m3.d
2.599
2.677
3.71
2.64
2.516
Humidity rate:%
1.910
1.524
1.77
1.46
1.85
grade:%
53.76
57.71
58.10
58.08
58.21
Wind temperature: °C
1127
1125
1037
1072
1074
Clinker rate:%
92.36
92.49
92.21
91.59
93.02
Iron making process energy consumption: kgce/t
429.49
426.84
438.59
440.60
466.20
Table 3 Energy consumption and technical and economic indicators of 2# blast furnace blower
project
Fan power consumption kW
Operating pressure kPa
Actual air volume m3/min
Utilization factor t/m3•d
Wind temperature °C
Focal ratio kg/t
Pulverized coal ratio kg/t
Rich oxygen m3/h
Transformation of the former
6200
270
1700
2.510
1,000
415
130
1500
After transformation
5000
275
1750
2.870
1130
399
143
1550
5.2 After the blower energy-saving renovation, the reasonable air supply system for blast furnace air supply system has been improved to achieve reasonable distribution of gas flow, sufficient heat, good utilization rate, smooth furnace condition, uniform and active furnace hearth, qualified molten iron quality, and favorable furnace type. And equipment maintenance requirements. After the transformation of the blast furnace blower by the high-voltage frequency converter, according to changes in the production process, the blast furnace air supply system will become more perfect.
5.2.1 Can quickly adjust the air volume Increase the air volume will increase the comprehensive smelting intensity. When the fuel ratio is reduced or the fuel ratio remains unchanged, the air volume increases, the material feeding speed increases, and the pig iron production increases. When the material speed exceeds the normal regulations, the air volume should be reduced in time. When the blast furnace is suspended, broken or low feed lines, it is necessary to reduce the wind in time and reduce it to the required level at one time. When the slag is not out of the net, the wind reduction should pay close attention to the condition of the tuyere to prevent the slagging of the tuyere. When the condition of the furnace turns smoothly and it is necessary to add air, it cannot be put in place once to prevent the blast furnace from being crushed. The duration of the two air additions can be quickly adjusted.
5.2.2 Effectively Adjusting the Air Temperature Increasing the air temperature can significantly reduce the coke ratio. Increasing the hot air temperature by 100°C can reduce the iron-making coke ratio by 15 kg/t. Increasing the air temperature can increase the kinetic energy of the blast, increase the temperature of the hearth and the active hearth, promote the initial distribution of the gas flow, and improve the effect of the injected fuel.
5.2.3 Can quickly adjust the wind pressure Wind pressure directly reflects the adaptability of gas and material column gas permeability in the furnace. The traditional method of high top pressure and low pressure difference is gradually optimized to the operation method of low top pressure and high pressure difference under the condition that the capacity of the whole wind of the wind turbine is allowed. The large air volume operation can be realized quickly, and the material speed of each furnace is generally accelerated. Increase, reduce the effect of the coke ratio, improve the utilization factor of the blast furnace.
5.2.4 Oxygen-enriched blast air control Oxygen enrichment can increase smelting intensity and increase production. Oxygen enrichment was increased by 1%, and production was increased by 4.76%. The theoretical combustion temperature of the tuyere was increased by 35-45°C, allowing more coal injections of 10-15kg/t, a lower coke ratio of 1%, and a gas heating value of 3.4%. The oxygen-enriched blast can increase the theoretical combustion temperature of the tuyere, which is beneficial to increase the temperature of the hearth and compensate for the decrease of the theoretical combustion temperature caused by coal injection. Increasing the oxygen content of the blast helps to improve the combustion of the injected fuel. Oxygen-enriched blasts can only be carried out when the furnace conditions are good. In the case of large injections, when the blast furnace stops spraying coal or when the amount of coal is substantially reduced, oxygen reduction or oxygen shutdown should be performed in time.
6 Benefits of frequency conversion retrofit of blast furnace blower According to the operating frequency and frequency conversion energy saving test record data provided by the user from August 1, 2008 to September 2, 2008, the frequency conversion speed regulation system generally operates at 40 to 48 Hz after adopting frequency conversion transformation. In normal production, the operating frequency is generally 45~46Hz, and the corresponding input operation power consumption is about 5000kW.h; the average power consumption of the power frequency of the user's frequency conversion device in the past year is 6200-6500kW.h, and the calculation of the energy saving rate is reduced. Small input power: 6200-5000=1200 (kW.h)
Energy Saving Ratio: (1200/6200)×100%=19%
After the speed control system is put into operation, it is estimated that the annual energy saving can reach 8.6 million kW.h after the annual operation of 7000 hours, and the domestic industrial electricity consumption can be calculated from 0.5 to 0.7 yuan, and the annual electricity savings can reach more than 4 million yuan. From energy-saving data, it can be seen that the application of high-voltage variable-frequency speed control systems to blast furnace fans is significant.
The WIN-HV series ultra-large capacity high-voltage frequency conversion has achieved great success in the blast furnace blower transformation of the company, breaking the successful application record of the domestic high-voltage inverter high power capacity, advanced control, and pioneering for domestic counterparts. The equipment has been safely and stably operated for 22 months since it was put into operation, which has improved the economic operation index and air supply system of the blast furnace, achieved the expected energy-saving effect, reduced the maintenance of motors, fans and dampers, and facilitated on-site operation and improvement. The automation level of the entire process ensures the normal production of the blast furnace. At the end of 2008, the user again selected the WIN-HV-046T100 high-voltage variable-frequency speed control system to carry out the energy-saving transformation of the 630kW induced draft fan of the blast furnace flue gas dust removal processing system. The power-on rate reached 30% at a power-on success.
7 Conclusion Shenzhen Micro Energy Technology Co., Ltd. has always been committed to the technical innovation and development of the inverter as its mission, in the past 5 years in the low-voltage inverter, medium-voltage inverter and high-voltage inverter in the high-power and high-performance development and The application has made outstanding contributions. The complete product line of micro-energy inverter has become the mainstream supplier of energy-saving and emission-reduction equipment for electric motors in China's industrial sector. It responds to and supports the nation's energy-saving and emission reduction mission goals as soon as possible, truly reflecting the company's return to nature for the planet. The concept of social value for saving energy for the motherland.
References [1] Blast Furnace Hot Blast Furnace Operation, Liu Quanxing, Beijing Metallurgical Industry Press.
[2] WIN-HV Series Micro Energy High Voltage Inverter Specification, Shenzhen City Micro Energy Technology Co., Ltd.
About the author: Qiu Zenghong is currently working in the marketing department of Shenzhen Micro Energy Technology Co., Ltd., engaged in the application and promotion of frequency converters.