An underwater drone is a device that can be moved underwater, has a visual and sensory system, uses a robot or other tool to replace or assist a person to perform underwater tasks by remote control or autonomous operation. In the 1970s, underwater drones have been greatly developed, and a number of robots capable of working at various depths and performing various operations have been developed, which can be used for oil exploration, seabed mineral deposit investigation, salvage operations, Pipe laying and inspection, cable laying and inspection, marine aquaculture and dam inspection of rivers and reservoirs.
Underwater UUV, Unmanned Underwater Vehicle can be divided into three categories: one is a submerged drone, the custom is called Towing Underwater Vehicle (TUV), and the other is remote control. The Remote Operated Vehicle (ROV); the other is the submarine-free drone, which is accustomed to be called the Autonomous Underwater Vehicle (AUV). From the first generation of deep submersibles of the 1960s, the evolution of ROV (70s), AUVs (80s) and hybrid types of Hybrid Vehicles has been passed.
Underwater drone control problemThe underwater drone is a rigid body with six degrees of freedom moving in water. It is itself a strongly coupled nonlinear system; due to the movement in the water, the hydrodynamic (resistance) coefficient is proportional to the square of the moving speed; Propulsion, the thrust is proportional to the square of the propeller speed. All of this makes the control problem very difficult, especially when it is required to perform the work at the fixed point, the above-mentioned reason causes the phenomenon of “zero gain, zero damping†at zero speed, making the rigidity of the dynamic positioning control system difficult to meet the requirements of the fixed point operation. . This is a question to be studied. Figure 3 shows the control principle of two underwater drones.
Submersible: A submersible is a sports carrier that carries observation and work tool equipment. The buoyancy block above the open frame structure ensures that the buoyancy of the water is substantially zero when the submersible is fully loaded; the propeller is installed in the horizontal, lateral and vertical directions to achieve three-dimensional motion. Place the gimbal at the front of the frame or where necessary, with a TV camera and lights on it. Conventional sensors include: imaging sonar, compass, depth pressure sensor, altimeter, and the like. The underwater electronic unit includes: an underwater computer, a drive, and a control module, which are installed in a sealed chamber at atmospheric pressure. The sensing components required for system monitoring include: power, pressure, temperature, water leakage, and the like.
Repeater: In order to quickly and accurately deliver the submersible to the predetermined working water depth and recover it to the surface quickly, and to reduce the resistance of the mother ship's swing and the current resistance of the umbilical cable to the submersible movement and operation, Interference and impact, generally have a cable remote control underwater drone configuration repeater. The cable is stored in the repeater and is equipped with a tethered retractable mechanism. The submersible is interlocked with the repeater when it is not in operation.
Draw system: used to place and recycle repeaters and submersibles. The hoisting system is usually gate-shaped, hydraulically driven, and has a storage mechanism and umbilical cable storage.
Tether: Used for mechanical soft connection and energy feed and information transfer between the submersible and the repeater. The tether is threaded over the buoyant material to make it buoyant in the water, thereby reducing the interference of the flow resistance on the body.
Armored main cable: The function of mechanical soft connection, energy transmission and information transmission between the hanger and the repeater. It is a steel wire armor structure to simultaneously hang the steel cable.
Observing the working equipment: installing a camera, imaging sonar on the motion carrier, and forming a basic system of the carrier. When you need to work, you can add 1-2 underwater robots and a variety of underwater working tools.
Underwater drone communication problemThere are two systems directly related to communication: monitoring systems and monitoring systems. The former mainly refers to equipment used for underwater search and underwater observation of underwater drones, generally including underwater cameras, pan/tilt and illumination, imaging sonar, acoustic and magnetic positioning systems. The latter mainly refers to the sensing equipment needed to intervene in the underwater drone motion control and guarantee the normal operation of the system, generally including depth gauge, altimeter, direction compass, temperature, pressure, voltage and current, etc., which can be collected by sensors, and Information transmission via wire or wireless. However, the only means of underwater communication are underwater sound and fiber. At present, from the domestic and international situation, the reliable communication rate of underwater sound is 1200 baud rate. The communication delay depends on the time it takes for the underwater sound to travel back and forth in the water. When the water depth is 6000 meters, the transmission time is 8 seconds. The distance traveled depends on the carrier frequency used and the power delivered, which is a significant limitation for underwater drones. Communication delay is a problem that cannot be overcome intrinsically. Therefore, how to increase the communication distance in the case of power limitation will be a major problem. At present, the communication distance is only ten kilometers. As the communication distance increases, the operating range of the AUV can also increase. The use of underwater acoustic information to achieve monitoring must overcome the difficulties caused by transmission delays. The picture on the right is an example of a hydrophone.
The hydrophone system hydrophone system is a passive acoustic system that uses four RESON TC4013 modules and an Analog Devices SHARC-21369 to determine the relative direction of the underwater acoustic wave transmitter. It has multiple underwater acoustic transmitter discrimination capabilities in the range of 20-35 kHz, but can only listen and track a selected frequency. The hydrophone provides information on the accuracy of the computer and altitude information ±1, which is used in the task of navigating to the acoustic transmitter.
The optical fiber is generally used for the underwater drones TUV and ROV with cables, and is composed of an optical transceiver (water surface), an underwater optical transceiver, and an optical cable. The advantage is that the data rate is high (100 Mbit/s) and it has good anti-interference ability. Disadvantages limit the working distance and maneuverability of underwater drones.
Underwater laser communication uses the blue-green laser with the lowest absorption rate of seawater medium, and has reached the sea-air communication distance of 100 meters deep, but it is still in the experimental stage, with large power consumption and volume, low efficiency and practicality to be improved.
Energy issues have always been a major factor limiting the scope of AUV operations, and research and development of energy sources with high energy rates is a long-term effort. In the foreseeable future, batteries are an option. It is possible to use batteries with variable half-life nuclear fuel in the future. Before these problems are solved, the aforementioned recycling device can be used as a relay station to perform underwater charging, so that two AUVs can be alternately charged to realize indefinite underwater operation. Of course, this does not solve the wide range of work problems of AUV. The following are the different energy requirements for ROV and AUV.
The ROV underwater drone supply voltage is usually related to the power and working depth of the underwater drone. As the depth increases, high-voltage power transmission and power equipment are required. In order to reduce the size and weight of the umbilical cable, ROV will adopt a higher voltage level in the future. These will provide AC power from the surface of the water. Generally, small and medium-sized underwater drones are powered by 220V, 50-60Hz single-phase AC power, and large-scale underwater drones use three-phase AC of 3000v or more to supply power to the underwater carrier.
The AUV itself carries a battery. In the early days, a sealed lead-acid battery was used. Now, a high-energy silver-zinc battery is used.
The development of a new generation of underwater UAVs is becoming more and more mixed, combining the advantages of ROV and AUV. For example, the ROV requirement is that the water depth is generally 6000 meters. Second, the control system uses large-capacity computers to implement processing data and digital control. Third, the manipulator on the submersible uses a multi-functional, force feedback monitoring system: The fourth is to increase the number and power of the propeller to improve its top-flow capability and maneuverability. In addition, special attention is paid to the miniaturization of the submersible and the improvement of its observation capability. In addition to the above common features, the AUV will continue to improve its autonomy and survivability, and avoid losing the biggest problem faced by this cableless submersible. From the development of key technologies we can describe as follows:
1 Energy technology Proton exchange membrane fuel cell has the performance required for the power unit of the underwater drone. The battery is characterized by high energy density, efficient generation of electrical energy, low heat during operation, and rapid start-up and shutdown [9]. The battery technology challenge is a suitable quiet pump, gas piping arrangement, heat dissipation, solid electrolyte, and efficient storage of fuel and oxidant.
2 Precise positioning technology At present, underwater UAVs use GPS on the water, and underwater positioning uses acoustic positioning equipment. Underwater GPS technology is currently developing rapidly, and the accuracy of autonomous navigation is expected to increase 10 times in 5 years.
3 Zero-visibility navigation technology Water mixing has always been the biggest obstacle to underwater UAV applications. Acoustics, laser technology and computer graphics enhancement technology will solve this problem.
4 Material technology Every 10m increase in water depth in the water, the external pressure will increase by 1 atmosphere (0.1MPa). High-strength, lightweight, corrosion-resistant structural materials and buoyancy materials are the key technical issues for underwater drones.
5 Operation Technology The development goal of underwater drones is to replace people in various underwater operations. The development of flexible underwater manipulators, special underwater working tools, and the sense of presence and virtual reality will make underwater UAVs play a greater role in marine development.
6 Acoustic technology is known as the latest "vector transduction technology" of the acoustic technology revolution, which enables the tracking distance of autonomous underwater drones to reach more than 100km. The low-frequency underwater acoustic communication technology can make the underwater communication distance reach more than 1000km, and the underwater transmission distance of the image can reach more than 20km. The development of underwater acoustic technology will make underwater drones truly "a thousand miles".
7 Intelligent technology machines have the same intelligence as people or more than human intelligence is a science fiction movie. From the current development level of machine intelligence, it still needs a long way to go. Underwater drones that are involved or semi-autonomous are a realistic solution to the current complex underwater operations.
8Recycling technology The underwater recycling operation of underwater drones is generally carried out near the sea surface, so it is often restricted by sea conditions and becomes a major factor affecting the underwater operation of underwater drones.
Lock Motor product introduction:
Safe Lock Motor, also known as The anti-theft lock motor, in the field of electronic Lock technology, Safe Lock Motor is a mechanical Lock components associated with the electronic control unit of the important parts.
Functions: it is widely used in various intelligent locks, such as Shared bicycle lock, fingerprint lock, glass lock, safe lock, hotel lock, family lock, inductive smart lock, etc
Features: Motor For Safe Lock is based on micro precision reducer development, small intelligent micro precision reducer can do 10 mm in diameter, is widely used in safe, locks, smart locks, sensor intelligent lock;
This kind of motor has the characteristics of low noise, low energy consumption, small volume, light quality, high precision, large torque and durability
Method of use: the best stable in horizontal plane, installed on the Safe Lock Motor output shaft parts, cannot use a hammer to knock, knock prone to press into the dc Safe Lock Motor drive, may cause damage to internal components, and cannot be used in the case of blocked.
Operating temperature range:
Gear Motor For Safe Lock should be used at a temperature of -10~60℃.
The figures stated in the catalog specifications are based on use at ordinary room temperature catalog specifications re based on use at ordinary room temperature (approximately20~25℃.
If a Safe Lock Motor is used outside the prescribed temperature range,the grease on the gearhead area will become unable to function normally and the motor will become unable to start.Depending on the temperature conditions ,it may be possible to deal with them by changing the grease of the motor's parts.Please feel free to consult with us about this.
Storage temperature range:
Gear Motor For Safe Lock should be stored ta a temperature of -15~65℃.
In case of storage outside this range,the grease on the gearhead area will become unable to function normally and the motor will become unable to start.
Service life:
The longevity of Dc Motor For Safe Lock is greatly affected by the load conditions , the mode of operation,the environment of use ,etc.Therefore,it is necessary to check the conditions under which the product will actually be used .The following conditions will have a negative effect on longevity.Please consult with us should any of them apply.
â—Use with a load that exceeds the rated torque
â—Frequent starting
â—Momentary reversals of turning direction
â—Impact loads
â—Long-term continuous operation
â—Forced turning using the output shaft
â—Use in which the permitted overhang load or the permitted thrust load is exceeded
â—A pulse drive ,e.g.,a short break,counter electromotive force,PWM control
â—Use of a voltage that is nonstandard as regards the rated voltage
â—Use outside the prescribed temperature or relative-humidity range,or in a special environment.
â—Please consult with us about these or any other conditions of use that may apply,so that we can be sure that you select the most appropriate model.
when it come to volume production,we're a major player as well .each month,we rurn out 600000 units,all of which are compliant with the rohs directive.Have any questions or special needed, please contact us, we have the engineer group and best sales department to service to you
Looking forward to your inquiry. Welcome to our factory.
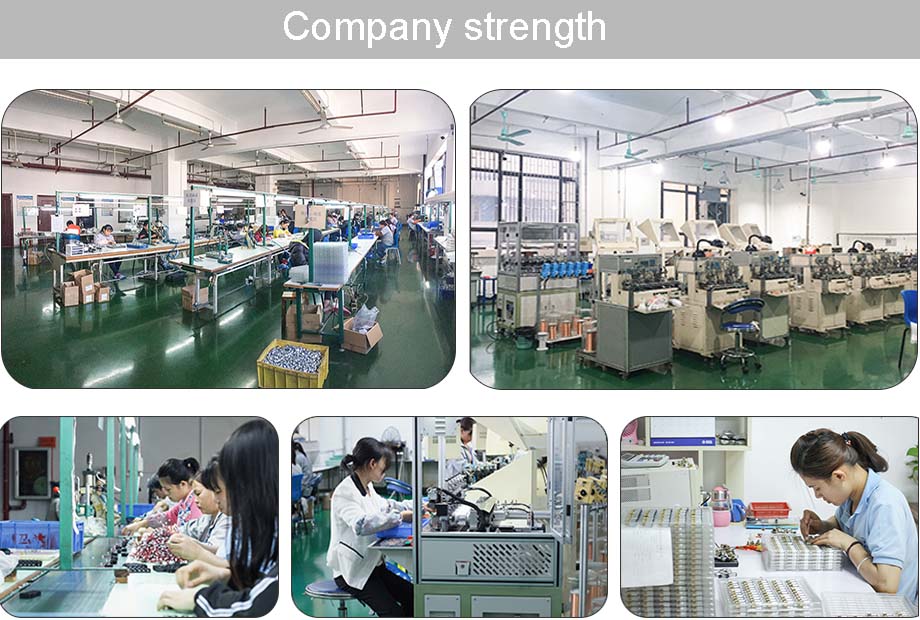
Safe Lock Motor,Motor For Safe Lock,Dc Motor For Safe Lock,Gear Motor For Safe Lock
Shenzhen Shunchang Motor Co., LTD. , https://www.scgearmotor.com